作為新能源汽車生產(chǎn)線的一線操作人員,電機(jī)鋁殼與定子轉(zhuǎn)子的熱套裝配是我每天都要接觸的關(guān)鍵工序。最近車間引入的 25 千瓦高頻感應(yīng)加熱機(jī),徹底改變了傳統(tǒng)加熱方式的效率瓶頸,40 秒將鋁殼內(nèi)孔加熱到 160℃的操作技巧,值得和同行們分享實(shí)際應(yīng)用心得。
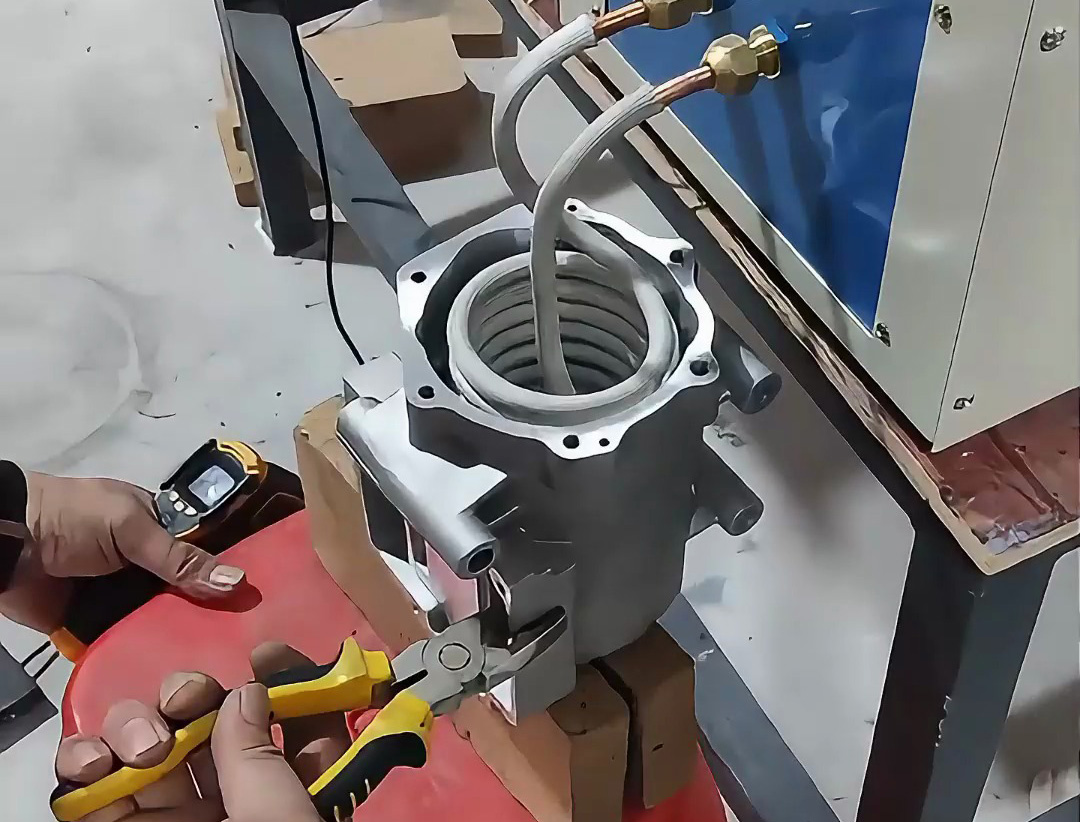
第一次接觸這套設(shè)備時(shí),最直觀的感受是「快」和「準(zhǔn)」。設(shè)備主體分為高頻電源柜和可拆卸式感應(yīng)線圈,我們常用的線圈內(nèi)徑適配 Φ80mm 鋁殼,接通 380V 電源后,只需三步就能啟動(dòng):
- 參數(shù)預(yù)設(shè):在控制面板輸入目標(biāo)溫度 160℃,系統(tǒng)自動(dòng)匹配 80kHz 頻率和 25kW 功率
- 鋁殼定位:將鋁殼內(nèi)孔對(duì)準(zhǔn)線圈中心,用工裝固定確保間隙均勻(約 5mm)
- 一鍵加熱:按下啟動(dòng)鍵后,紅外測(cè)溫屏實(shí)時(shí)跳動(dòng),40 秒準(zhǔn)時(shí)停機(jī)
和以前用的電阻爐相比,省去了提前 1 小時(shí)預(yù)熱的步驟,而且加熱過程中鋁殼外壁幾乎不燙手,安全隱患明顯降低。
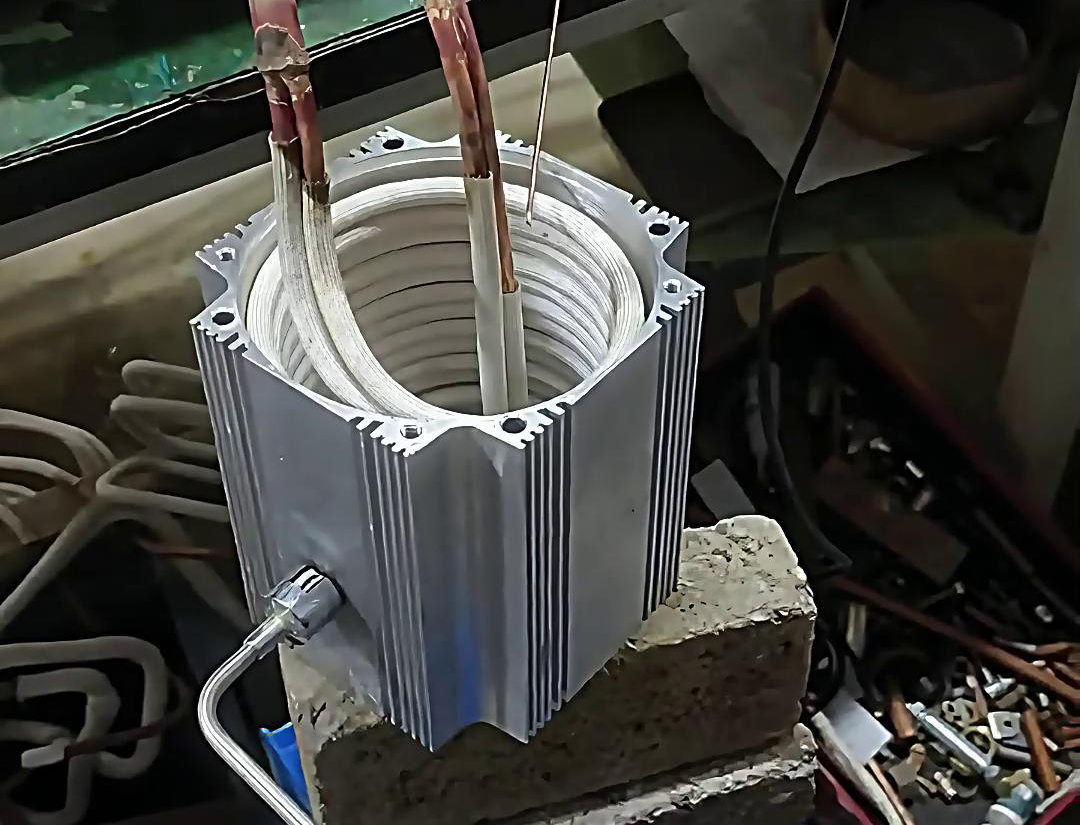
加熱完成到壓裝的時(shí)間窗口非常關(guān)鍵。根據(jù)多次實(shí)操總結(jié):
- 10 秒黃金期:加熱結(jié)束后,鋁殼內(nèi)孔膨脹量達(dá)到峰值(約 0.08mm),此時(shí)迅速吊裝定子插入,壓裝力最?。▽?shí)測(cè)約 12kN)
- 溫度監(jiān)測(cè):如果超過 20 秒再裝配,溫度下降到 140℃以下,膨脹量縮減到 0.05mm,需要增大壓裝力(約 18kN),且容易出現(xiàn)異響
車間還摸索出「二次加熱」技巧:當(dāng)鋁殼壁厚超過 8mm 時(shí),先加熱 30 秒至 120℃,停頓 5 秒讓熱量擴(kuò)散,再加熱 10 秒到 160℃,這樣能避免外層過熱而內(nèi)層溫度不足。
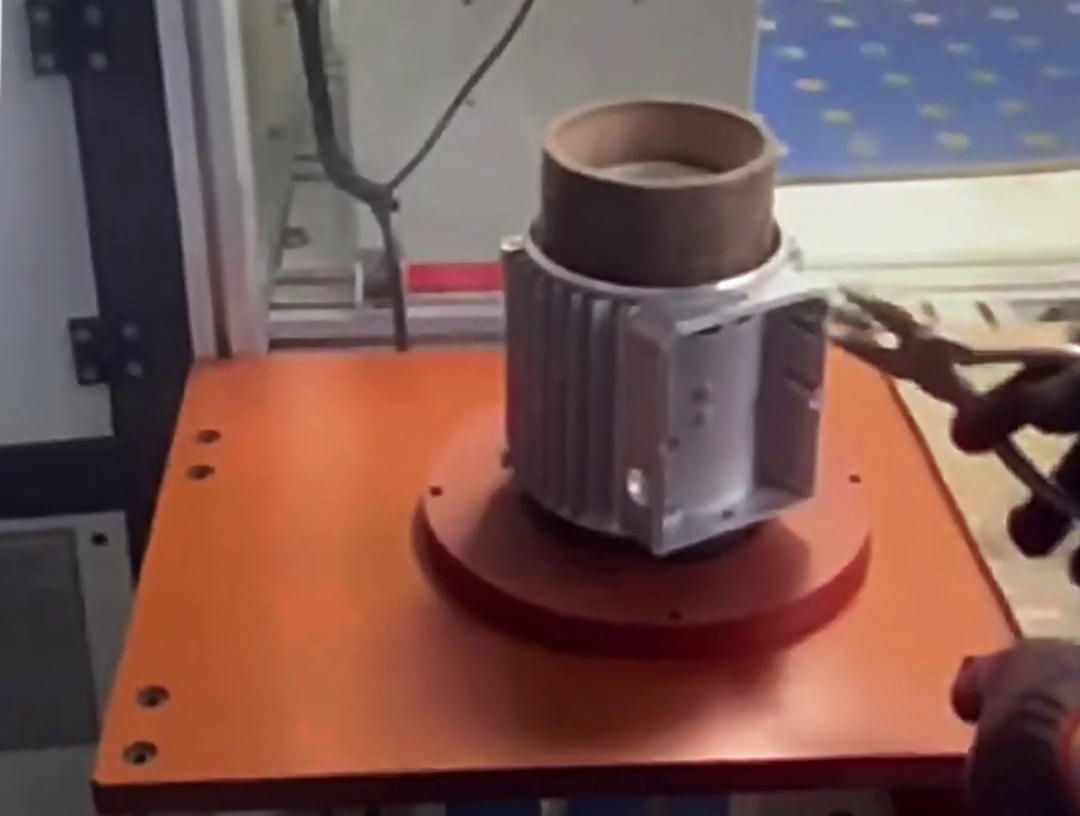
設(shè)備運(yùn)行三個(gè)月來,遇到過兩次典型問題:
溫度超調(diào)報(bào)警
- 原因:線圈匝間有鋁屑?xì)埩?,?dǎo)致局部磁場增強(qiáng)
- 解決:用壓縮空氣吹掃線圈,并用酒精擦拭,后續(xù)增加產(chǎn)前線圈檢查工序
加熱時(shí)間延長
- 原因:冷卻水路結(jié)垢,線圈散熱不良導(dǎo)致功率受限
- 解決:每周用 5% 檸檬酸溶液循環(huán)清洗水路,現(xiàn)在改為用去離子水,再也沒出現(xiàn)過類似問題
這些經(jīng)驗(yàn)讓我們把設(shè)備綜合效率(OEE)從最初的 75% 提升到 89%。
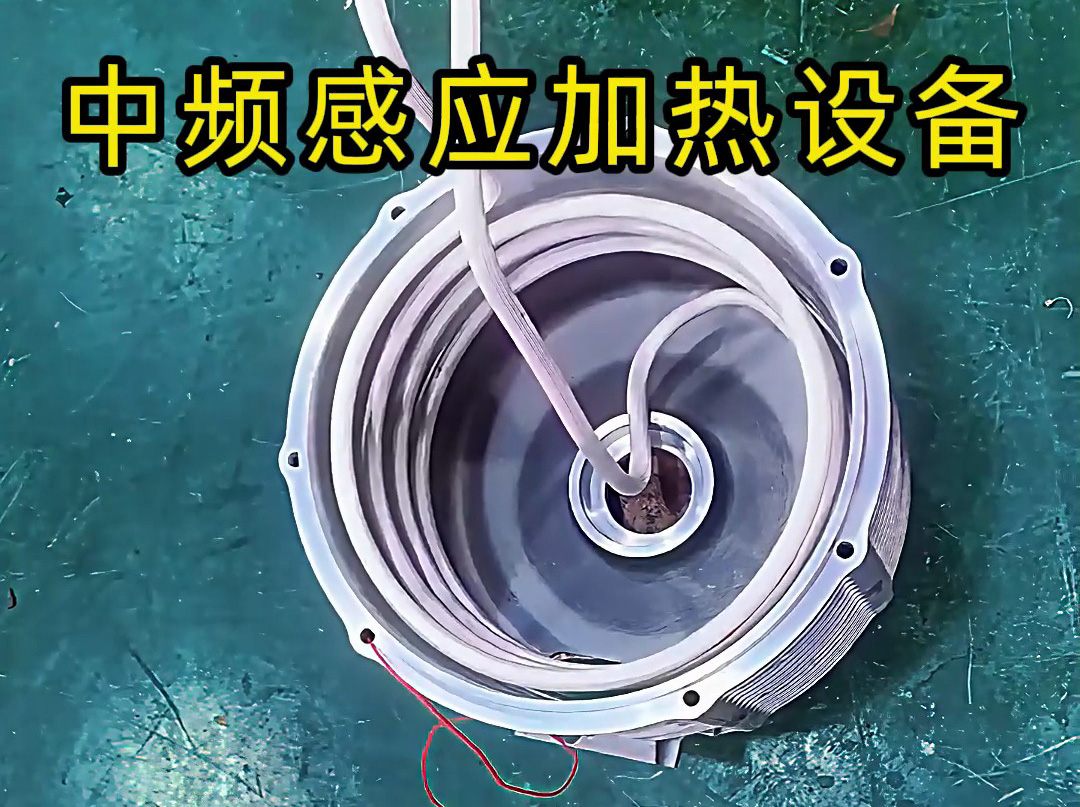
用表格整理了兩種工藝的實(shí)際數(shù)據(jù),更能看出差異:
指標(biāo) | 傳統(tǒng)電阻爐加熱 | 高頻感應(yīng)加熱 |
---|
單件加熱時(shí)間 | 120 秒 | 40 秒 |
能耗 | 0.6kWh | 0.28kWh |
內(nèi)孔溫差 | ±15℃ | ±5℃ |
壓裝合格率 | 92% | 99.3% |
最明顯的是壓裝后的同軸度檢測(cè),高頻加熱的鋁殼能把誤差控制在 0.03mm 以內(nèi),這對(duì)電機(jī)噪音控制至關(guān)重要(實(shí)測(cè)噪音降低 3dB)。
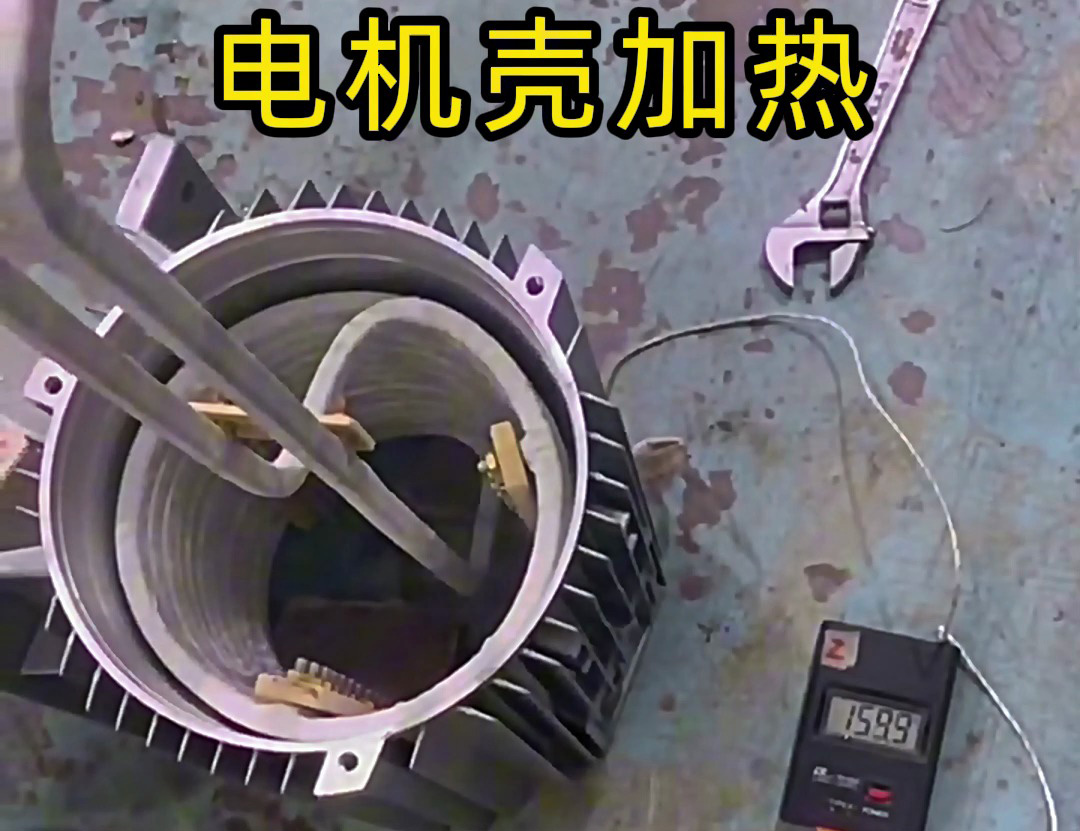
現(xiàn)在班組里形成了三個(gè)操作共識(shí):
- 聽聲音:加熱時(shí)線圈發(fā)出的高頻噪音變沉悶,可能是鋁殼擺放偏斜,需要立即停機(jī)調(diào)整
- 看顏色:鋁殼內(nèi)孔加熱到 160℃時(shí),表面氧化膜會(huì)呈現(xiàn)均勻的暗灰色,局部發(fā)白說明過熱
- 記數(shù)據(jù):每批次記錄壓裝力曲線,異常波動(dòng)能提前發(fā)現(xiàn)線圈老化等潛在問題
這套高頻加熱工藝讓原本需要兩個(gè)人配合的工序,現(xiàn)在一人就能操作,而且每天多產(chǎn)出 120 臺(tái)電機(jī)。對(duì)新能源汽車制造來說,這樣的裝配細(xì)節(jié)積累,正是產(chǎn)能爬坡期的關(guān)鍵支撐。
|